What are the “Statuses” and life cycle of a Production Order in D365 Finance and Operations ?
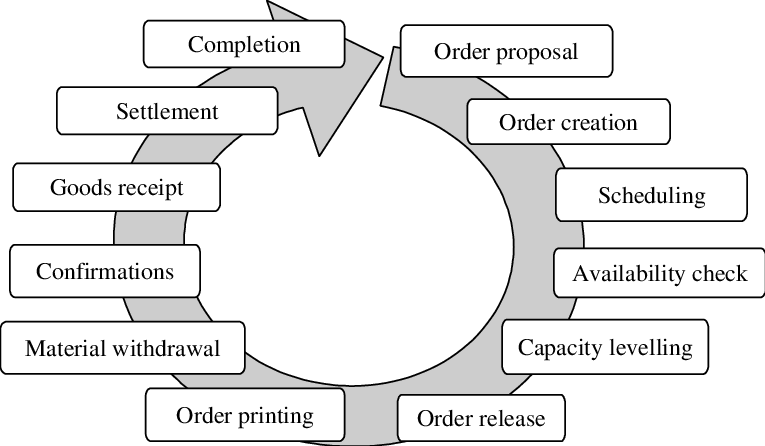
A Production Order in D365 F&O (Finance & Operations) represents a document that authorizes the manufacturing of a specific quantity of a product. It’s the core document that drives the entire manufacturing execution process. Let me walk you through its complete lifecycle in detail.
Overview of Production Order Purpose
Before diving into the steps, it’s important to understand that a production order serves as the central control mechanism for manufacturing activities. It tracks material consumption, labor usage, machine time, and ultimately the cost of producing finished goods. The production order connects planning (what needs to be made) with execution (actually making it) and financial tracking (what it cost to make).
The Production Order Lifecycle Stages
The production order follows a specific status progression that controls what activities can be performed at each stage. Each status change triggers different system behaviors and enables different functionalities.
1. Created Status
When a production order is first generated, either manually or through master planning, it enters the “Created” status. At this stage, the order exists in the system but no physical activities have begun. The system performs several key actions during creation:
The BOM (Bill of Materials) is copied from the item’s production BOM, creating a production BOM specific to this order. This allows modifications without affecting the master data. The route is similarly copied from the item’s production route, establishing the sequence of operations needed to manufacture the item. The system also assigns a production order number based on the configured number sequence.
During the created stage, you can still make fundamental changes to the order, such as modifying quantities, changing dates, or even switching to a different BOM or route version. No inventory transactions or capacity reservations have occurred yet, providing maximum flexibility for adjustments.
2. Estimated Status
Moving to “Estimated” status triggers the first major calculation process. The system performs a complete cost estimation based on the BOM components, route operations, and current cost data. This estimation includes:
Material costs are calculated by exploding the BOM to determine all required components and their quantities, then multiplying by current cost prices. The system considers scrap percentages and yield factors during this calculation. Labor costs are computed based on the route operations, their run times, and the cost categories assigned to the resources. Overhead costs are applied according to the costing sheet configuration, which might include both direct and indirect overhead allocations.
The estimation process also performs a net requirements calculation, checking inventory availability for all components. This helps identify potential material shortages before production begins. The estimated costs serve as the baseline for variance analysis once production is complete.
3. Scheduled Status
Scheduling represents a critical planning phase where the system determines when and where production will occur. D365 F&O offers two scheduling methods, each with different levels of detail:
Operations scheduling works at the operation level, assigning operations to resource groups and calculating start/end times based on available capacity. This method is faster but less precise, suitable for longer-term planning. It considers the route’s operation sequence, operation run times, and resource group capacity but doesn’t assign specific resources.
Job scheduling provides more granular planning by breaking operations into individual jobs and assigning them to specific resources. This method considers setup times, queue times, transportation times between resources, and overlap possibilities between operations. Job scheduling creates a detailed minute-by-minute plan but requires more processing time and is typically used for near-term execution planning.
Both scheduling methods respect capacity constraints, working calendars, and efficiency percentages. The system can perform forward scheduling (from a start date) or backward scheduling (from a required completion date).
4. Released Status
Releasing a production order marks the transition from planning to execution. This status change authorizes the shop floor to begin work and triggers several important system actions:
Picking lists are generated for all BOM components, creating warehouse work to move materials to the production input location. The system considers the flushing principle of each component – whether it should be manually picked, backflushed during operation reporting, or consumed at order start/finish. Route cards or job cards are printed, providing shop floor workers with detailed instructions for each operation. These documents include operation descriptions, resource assignments, time estimates, and quality instructions.
The release process also performs availability checking to ensure all required materials and resources are available. If shortages exist, the system can prevent release or allow it with warnings, depending on configuration. Capacity reservations become firm at this point, blocking the scheduled time slots on resources.
5. Started Status
Starting a production order indicates that physical production has begun. This status change enables several key functionalities:
Material consumption transactions can be posted, either through picking list journals or automatic backflushing. Time and attendance integration activates, allowing workers to clock in/out on production jobs. Work-in-process (WIP) tracking begins, with costs accumulating as materials are consumed and labor is reported.
The system creates the first inventory transactions, moving materials from warehouse locations to WIP. If the BOM includes items with “Start” flushing principles, their consumption is posted automatically. The production order now appears in various shop floor control interfaces, ready for operation reporting.
6. Reported as Finished Status
This status indicates that some or all of the ordered quantity has been completed and is ready for receipt into inventory. The reporting process involves several steps:
Workers report completed quantities through various interfaces – the production journal, job card terminal, or mobile device. The system validates reported quantities against order quantities and configured over/under delivery tolerances. Quality orders may be triggered automatically based on quality associations, requiring inspection before the goods can be put away.
Report as finished transactions create inventory receipts, moving items from WIP to finished goods inventory. The system calculates actual production costs based on consumed materials, reported labor time, and applied overhead. These actual costs are compared to estimated costs to begin variance analysis.
7. Ended Status
Ending a production order finalizes all production activities and calculations. This comprehensive process includes:
All pending transactions are posted, including any remaining material consumption, time reporting, or overhead allocations. The system performs final cost calculations, determining the actual cost of goods produced. Variances between estimated and actual costs are calculated and categorized (material price variance, material usage variance, route variance, etc.).
WIP accounts are cleared, with balances transferred to finished goods inventory and variance accounts. The production order becomes read-only, preventing any further transactions. All capacity reservations are released, making resources available for other orders.
8. Costed Status (Optional)
Some organizations use an additional “Costed” status after ending, which performs final cost adjustments and locks the order completely. This status is particularly useful in standard cost environments where variances need review before posting to the general ledger.
Key Processes Within the Lifecycle
Throughout the production order lifecycle, several important processes occur:
Material Consumption: Components can be consumed through various methods – manual picking list journals, automatic backflushing based on operation progress, or batch consumption at start/finish. The system tracks both planned and actual consumption, enabling usage variance analysis.
Time Reporting: Labor and machine time can be reported through route card journals, job card terminals, or time and attendance systems. The system validates reported times against estimates and can enforce various controls like maximum time limits or required approval for significant overruns.
Quality Management: Quality orders can be triggered at various points – material receipt, operation completion, or final product completion. These orders can block further processing until quality results are recorded and approved.
Cost Accumulation: Throughout production, the system accumulates costs in WIP accounts. These include direct material costs, direct labor, machine costs, and allocated overhead. The cost accumulation follows the organization’s costing method (standard, weighted average, FIFO, etc.).
Integration Points
Production orders integrate extensively with other D365 F&O modules:
Master Planning generates planned production orders based on demand and converts them to firm orders within planning time fences. Warehouse Management handles material picking and finished goods put-away, potentially using advanced warehousing features like wave processing. Product Information Management provides the master data (BOMs, routes, resources) that production orders consume. Cost Accounting tracks production costs and calculates variances for management reporting.
Best Practices and Considerations
Successful production order management requires attention to several key areas:
Status progression should follow business rules – some organizations require approval workflows between certain status changes. Regular monitoring of orders stuck in intermediate statuses helps identify production bottlenecks. Proper setup of flushing principles, backflush points, and automation rules reduces manual transaction entry. Clear policies on handling variances, scrap, and co-products ensure consistent treatment across orders.
The production order lifecycle in D365 F&O provides a robust framework for managing manufacturing operations from planning through execution to cost analysis. Understanding each status and its implications helps organizations optimize their production processes and maintain accurate cost tracking throughout the manufacturing cycle.